A key part of managing the risks at an operating facility is ensuring that personnel are competent in their roles and understand how process safety management works in their organisation. Organisations such as the ISC (IChemE Safety Centre) have developed competence frameworks that map out process safety competence requirements for different roles. In reality, how many organisations deliver on process safety competency development? Do front-line staff get the same level of competence investment that management and engineering personnel get whilst they are the most exposed to potential events?
Process Safety training has been available in the market for over 20 years. There are numerous face-to-face training courses available that cater for different needs. They typically range from 1 to 5 days and the costs typically range from several hundred to thousands of dollars. Whilst much is gained in the interactions that occur between trainers and participants, the costs and logistics often are a significant barrier to developing the broader organisation's competence. Across the industry, we currently rely on developing process safety evangelists within our business as the key means of PSM delivery.
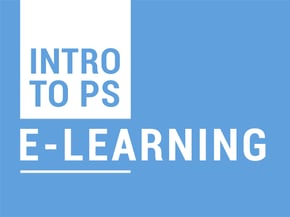
|
|
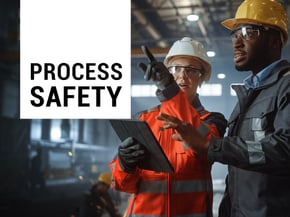
|
This INTRODUCTION TO PROCESS SAFETY online course is for all staff who work at hazardous facilities. FIND IT HERE! |
Find out more about the discounted PROCESS SAFETY ESSENTIALS PACK HERE! |
Prefer a face-to-face course? Find out about our next PROCESS SAFETY FOUNDATIONS course HERE! |
I have been running a process safety training business for over 15 years and see these dynamics time and time again. With internal staff movements and constraints on training spend, I have seen many companies not materially move forward over several years. Often when the evangelist moves on to a new role, there is a significant step backwards. How do we broaden out the skill pool so that every person associated with an operation understands the basics and can more effectively contribute to PSM? This is what is needed to shift the culture.
To deliver on competence development for the business, the following training model is proposed. It is fundamentally based on foundation training that the whole company receives.
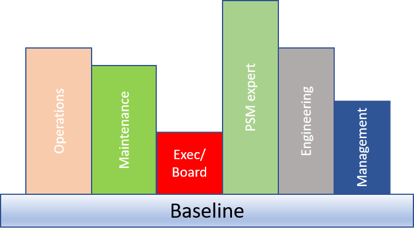
Key Points
- All staff associated with the operation should be trained to an introduction level and understand what good practice PSM look like. It is important that front-line staff can articulate effective PSM to their colleagues.
- Layer on organisational, facility and role-specific training to develop necessary skills to drive competence performance. Examples of this could include:
a) Operational PSM workshops for operators
b) Developing internal leadership capability at the technical level (HAZOP, LOPA etc)
c) Executive and board training on PSM due diligence
- Refresher and assessment to be part of the competence program.
To document the quality of your Process Safety Competency program, have a look at this checklist. We use it as part of our process safety audits.
DOWNLOAD PSM COMPETENCY CHECKLIST
|
We see e-learning as a part of the mix of deploying process safety training to the masses. Try module 1 of our process safety e-learning course here:
TRY PROCESS SAFETY E-LEARNING: MODULE 1
|